Back To Oil: Plastic To Fuel Pyrolysis Plant
Did you know that plastic products are manufactured from oil? Well, plastic can not only become oil by using waste plastic pyrolysis plant, but the fuel is useful for the revolution of making everything old new (and more useful) again.
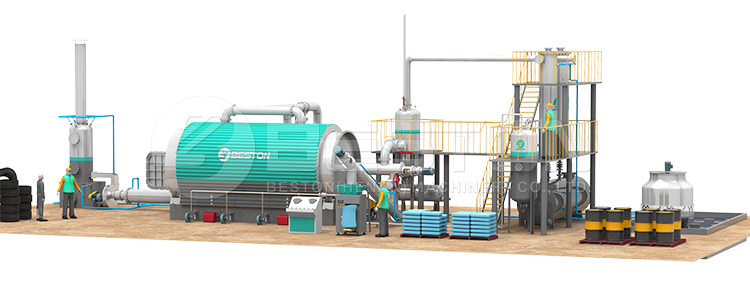
Though there’s a new twist on plastics, and even tyres, that make it possible through pyrolysis to transform them into fuels of many types. Here’s a bit more about how plastic oil conversion machine works, and what kinds of fuel it creates.
Waste Plastic to Fuel Oil Plant
The first question people want to know is how is this possible? The second is how does plastic become different kinds of fuel?
The second question is a great starting point. So, let’s start there. The process of turning the plastic back into oil different byproducts (or fuel types) are created.
Fuel oil makes up 45 percent of the byproduct from turning plastic to fuel pyrolysis plant. This oil is excellent for heavy oil generators that then crank out electricity.
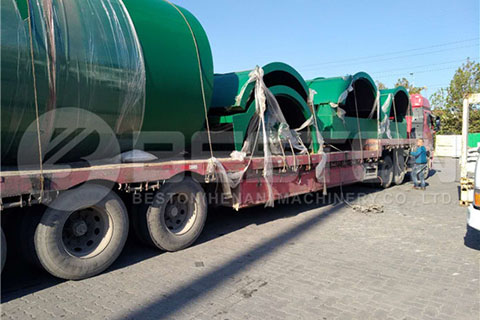
It can even be made into diesel and gasoline with the added use of waste oil distillation equipment. It is possible to also use the fuel for the plant reactor itself.
Carbon black makes up 40 percent of the byproduct, which can then be turned into coal or briquettes.
The combustible gas byproduct that makes up 15 percent of the fuel byproducts is excellent for furnaces and to heat reactors. It can be stored for heating fuel as well.
Plastic Pyrolysis Plant Design-How Does It Work?
The pyrolysis plants use their own equipment to create oil out of plastics. Add the plastic to the reactor automatically from the recycling source. The plastics can include items such as plastic bags and other plastics that otherwise would clog up landfills, or get turned into new plastic bottles.
The reactor gets heated up through fuel, which may contain the byproduct of the prior batch of plastics. At 100 degrees Celsius, oil is formed.Though the top temperature for the process is up to 280 degrees Celsius.
Different byproducts are made. Heavy oil gas, for instance, becomes a liquid and is dropped into a tank. Lighter gasses rise through the condensers.They can be stored for use later in the reactor or sold to industry for manufacturing, operating machinery, making electricity, making charcoal, and other ways fuel is consumed.
Anything that cannot be used, or is an incondensable gas goes back to the furnace to recycle. The reactor of a pyrolysis plant requires cooling down between batches. Though, it’s usually important to ensure that the reactor cylinder is not overfilled to allow space for the material to move.
Carbon black comes out at the very end of the process, following the cooling down period. At that point, exhaust should be on the low side and is only set free according to the guidelines, usually when it reaches a standard mark. That’s the basic overview of what and how pyrolysis works when turning plastic into fuel sources. More details can be found: https://beston.co.za/.